EDM Ceramics
Electrical Discharge Machining (EDM) was one of the first non-conventional machining manufacturing processes to be developed and arose from the concept of eliminating material that a part will present when it is subjected to a series of repetitive electrical discharges that take place between an electrode and the piece itself in the presence of a dielectric fluid, which allows the evacuation of the eroded particles.
Obtaining electrically conductive nanostructured ceramics that meet the necessary requirements to be machined by EDM is of great interest due to the extremely high hardness these kind of materials often feature and their very difficult and expensive machining using conventional techniques.
The EDM technique is also of great interest from a technological point of view since it allows the design of materials of great hardness and durability with complex structures and very small tolerances.
The machining of electroconductive ceramics requires the materials have electrical resistivities between 100-300 Wcm.
The CINN has developed nanostructured ceramic materials with high performance and excellent functional properties using a new colloidal processing routes. We use nanostructured raw materials, both oxidic (high hardness: alumina; high wear resistance: alumina-zirconia eutectic) and non-oxidic (Si3N4, TiC, TiN, TiB2, B4C, SiC, SiCw), which are subjected to a surface modification through colloidal processing that promotes afterwards the nucleation of nanocrystals on their surface thanks to a thermal treatment. This new processing route has been applied, for example, to the development of oxide/non-oxide nanocomposites, such as Al2O3/TiC/ SiCw (ATiSiCw), and non-oxide/non-oxide nanocomposites, Si3N4/TiN and Si3N4 sub>/TiN-TiB2. In these nanocomposites, the matrix is usually composed of hard materials such as alumina and/or abrasive ones such as the alumina-zirconia eutectic, which are doped with metal nanoparticles (Ni, Mo, W) in low concentrations to cause the hardening of the matrix itself. Then, the necessary quantities of nanoparticles with high electrical conductivity is added , according to the percolation theory, to ensure their EDM machinability. Some examples of pieces made using this last technique are shown in Figure 1.
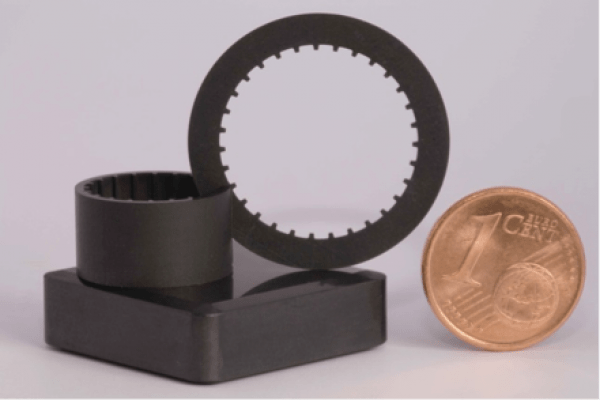
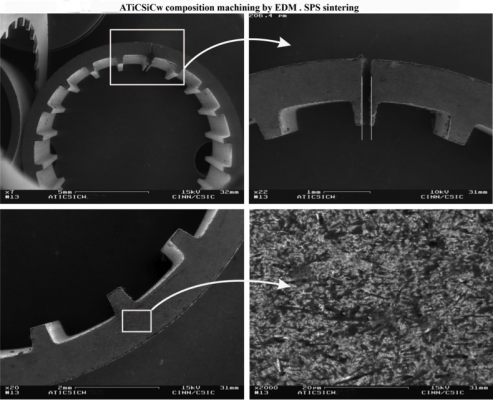